| | High-PAS™ - Testing After Saw | | USEA has developed proprietary technology for the highly parallel testing of parts after saw. Our technology
fixes the die in position after the sawing processes, with minimal x-y displacement. This allows for highly parallel testing of the die at temperatures ranging from
-55°C to 200°C on automated test equipment. | | High-PAS™ benefits our customers and collaborators both during their engineering and production phases by: | | | Increased Throughput (UPH) - When testing at high volume, USEA's High-PAS™ technology dramatically increases
the test speed for chip scale, bumped die, and singulated die on the film frame handler. This is achieved through elimination of jams associated with turret and
gravity feed handlers, reduced indexing time between tests, and reduced engineer supervision requirements. | | Reduced Tooling Costs - The tooling costs for handling chip scale packages on handlers such as turret and gravity
feed handlers are avoided when handling the parts on the film frame handler. | | Reduced Engineering Setup Costs - The engineering time required to implement a change kit on turret and gravity feed
handlers is eliminated and replaced with a lower effort alignment procedure on the film frame handler. | | Tri-Temperature Testing - USEA's film frame handler strategy allows for the testing of parts at multiple temperatures
ranging from -40°C to 85°C. | | Reduced Test Costs - The increased throughput of testing coupled with lower engineering setup costs and associated NRE results in
a lower test cost and higher customer margins. | | Test After Saw - The mechanical and chemical damage to parts that sometimes occurs during the saw process is screened for using the
High-PAS™ testing after saw technology. | | | | | |
|
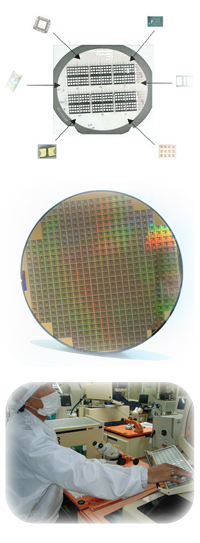 |
|
|
|