| | Case Study - Failure Analysis | | Business Challenge: | | A collaborator of USEA was recently observing an increased failure rate of a component and asked
USEA's Advanced Programs Group to investigate the issue and identify the root cause. | | USEA Solution: | | The background to the issue was: | | | All components were within specification as determined by temperature stress and parametric testing at USEA's Philippines
facility before they were released. | | The components ultimately were assembled into several products by our collaborator. | | The increased rate of failure was observed in only one product. | Upon understanding the issue the APG came up with a parallel investigation plan, as we understood that the issue
only manifested itself when the component were mounted into a specific final product and did not reveal itself when placed into other products. Our hypothesis was that,
'either the component had changed or the placement and testing of the component in the final product had changed'. To determine the root cause, two parallel
investigational tracks were opened. | | In Depth Failure Analysis. The initial work done by USEA involved an industry standard 8D investigation to determine
whether device fabrication or testing parameters had changed. Then the Advanced Programs Group undertook an advanced investigation that included: | | | Parametric data collection during temperature cycling, including a study to investigate whether parametric data drifted during
the tests. | | CSAM analysis to determine whether there was a mechanical failure or delamination in the components. | | Finite element modeling (FEM) to investigate how defects in the component assembly could result in failure during temperature cycling. | These investigations did not reveal any increased failure rates for the component. | | Downstream Analysis. USEA also sought to understand what happened to the component after it had been released by USEA. Through
detailed conversations with our collaborator and subcontractors, we discovered that the component was mounted onto the device board at a subcontractor's facility, subjected to temperature
cycling tests, and then functionally tested. It was at this point that the increased failure rates were observed. | | In the downstream analysis, it was discovered that the subcontractor had changed the soldering process for mounting the components on
the device board. They switched to RoHS compliant solder that required higher temperature. It was therefore our hypothesis that the root cause of the increased failure rates was
temperature-induced stress on the die during the soldering process. | | | | | | |
|
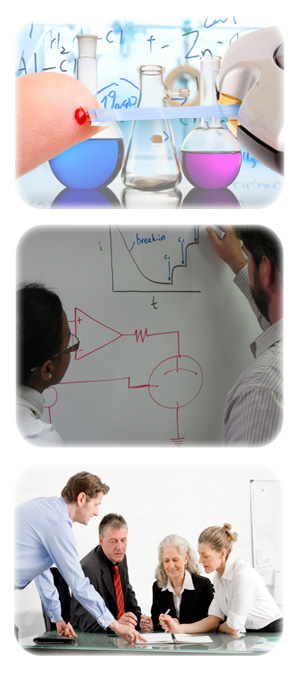 |
|
|
|